Saporito Finishing recently announced it has received a patent for its unique floating rack design for electroplating applications. The floating rack boosts plating quality, cuts costs, reduces labor, and speeds project turnaround on metal finishing projects. The new rack is ideal for use when plating tubes, components with blind holes, and cup-shaped parts in high-speed, automatic production operations.
Our new floating rack takes our metal finishing services to the next level, says Jeff Logan, president, at Saporito Finishing. It also helps us meet customer demands for higher quality, more cost-effective service, and faster turnaround. We can now process workpieces, like caps and cups, quickly and efficiently instead of manually plating them. From a company standpoint, the new floating rack boosts competitiveness and enhances customer service. It’s a win-win for everyone involved.

Two Common Methods of Plating
Electroplating bonds metal ions in solution to a metal substrate using electrodeposition. In this process, the flow of electrical current increases the ions’ attraction in the plating solution to the metal workpiece’s surface. The plating protects the workpiece from corrosion and wear, prolonging its useful life and boosting its aesthetic appeal. Selecting the right electroplating method for a workpiece, however, is critical. Two standard methods of plating workpieces are barrel plating and rack plating. Knowing when to use each is paramount.
With barrel plating, finishers place the parts in a barrel, which then spins slowly while immersed in the electroplating solution. Spinning causes the workpieces to tumble or cascade and provides a uniform coating to the workpieces. Barrel plating works well for plating a high volume of small, durable workpieces, such as stampings, fasteners, and small parts of similar shapes and sizes.
With rack plating, finishers hang individual workpieces to metal frames, hooks, or racks, sometimes using screws, wires, or other means. The rack holds the part securely in place during the electroplating process and provides the connection to bring electrical current to the part. Finishers use rack plating for delicate parts that can’t withstand a barrel’s tumbling action or for large or complex parts too big for a barrel. Rack plating is the “go-to” choice in industries where a high-quality finish is paramount, including military and defense, automotive, medical, and electronics.
Floating Rack Helps Beat Plating Challenges
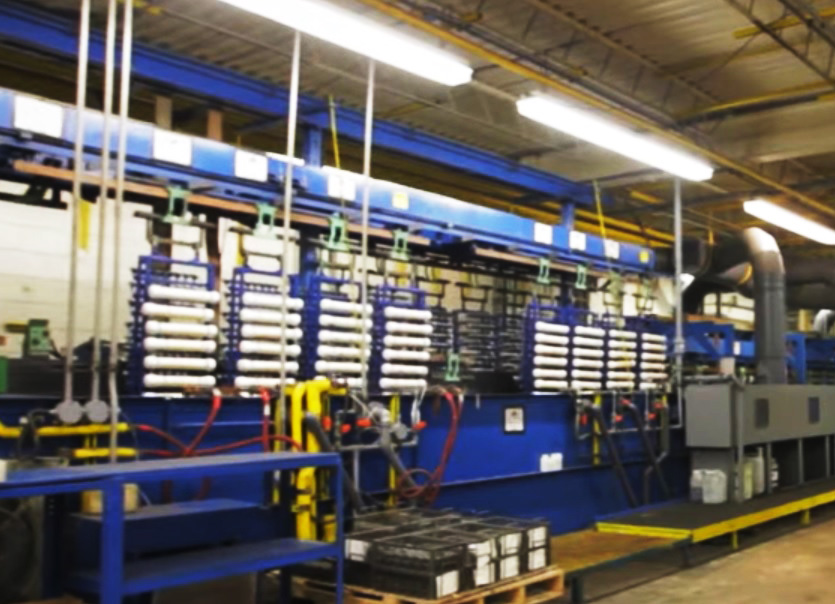
Some workpieces, however, present challenges for finishers using the rack plating process. Tubes, components with blind holes, and cupped shape parts are especially challenging for rack plating, especially in high-speed, automated operations. For example, if a finisher hangs a cup-shaped part right side up on a rack, the electroplating solution inside the cups can be carried from tank to tank, contaminating the other tanks further down the process. If the finisher hangs the cup upside down, not all of the part gets plated.
The plating solution only works on areas it touches, says Logan. If the solution doesn’t touch an area, it remains unplated and vulnerable to corrosion and wear. Tube assemblies, components with blind holes, and cupped shape parts have areas where it’s hard for the metal plating solution to reach, leaving gaps in coverage where the air pockets occur. Our new floating rack helps us eliminate these plating challenges and provides high-quality coverage of metal parts. The floating rack is especially beneficial when it comes to high-speed plating operations.”
Unique Design of Floating Rack Key
The key to the floating rack is its unique design. It allows for the workpiece’s rotational movement during the plating process automatically and without manually manipulating the part, which typically involves stopping the line and interrupting the process. That enables the plating solution to reach the part’s smallest crevices.
In addition to increasing finish quality, the floating rack also enhances the process tanks quality by reducing contamination from “drag-in” from tank to tank. Plus, the floating rack cuts labor costs, reduces turnaround, and increases throughput. Put simply, the floating rack helps Saporito produce a high-quality finished piece quickly and cost-effectively.
As a single-source supplier of finishing solutions, Saporito offers a premium line of metal finishing processes, including zinc plating, anodizing, zinc-nickel plating, electroless nickel plating, hard coat anodizing, magnesium anodizing. and many other finishes. It also provides aluminum treatment services, such as chemical film conversion and etch and clean.
Founded in the 1940s, Saporito strives to maintain the highest environmental standards possible, which the floating rack helps by reducing drag out to rinse tanks. The company is continually looking for advancements, like the floating rack design, to boost quality, cut costs, and shorten turnaround for customers while protecting the environment.