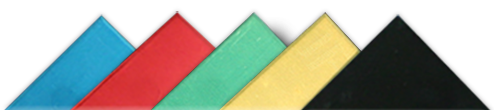
Anodizing Services
Sulfuric Anodize
The color will vary slightly with alloy. Aluminum with low alloying elements will show practically no color change. It is the best coating on aluminum for dyeing. Wrought sulfuric acid anodized parts can be dyed practically any color or shade. Sulfuric anodizing can withstand 336 hours neutral salt spray according to ASTM B117.
Chromic Anodize
The color of the Chromic Anodize coating varies from light gray to dark gray depending on the alloy. It is not as readily dyed as sulfuric anodize. The salt spray requirement is 336 hours using a 5% solution per method 811 of FED-STD-No. 151 or ASTM B117. The minimum weight for Type I coatings is 200 milligrams/sq. ft.
Chromic anodize is a thin coating that will scratch easily. Therefore, it can be used for inspection of aluminum forgings or castings by noting evidence of chronic acid bleed out from laps, cracks, seams, etc..
Hard Anodize
Hard Anodize color will vary from light tan to black depending on alloy and thickness. The Hard anodized coating can be dyed in darker colors depending on thickness. Hard anodize coating penetrates the base metal to a depth equal to the build up on the surface. The thickness measurement includes both the buildup and penetration. This process provides a very hard ceramic type coating and good dielectric properties. Abrasion resistance will vary with the thickness of coating. Where extreme abrasion resistance is required, parts should not be sealed, as some softening will occur. Hard anodize corrosion resistance is good. Where increased corrosion resistance is required, parts should be sealed in a dichromate solution.
For more information read our ‘Benefits of Hard Anodized Aluminum Coatings’ Case Study.
Lubricant, Solid Film
Solid film lubricant is used to prevent galling and seizure of metals. Lubricant covered by this specification is intended for use on aluminum, copper, steel and stainless steel, titanium, and chromium and nickel bearing surfaces. The process is useful where conventional lubricants are difficult to apply or retain, or where other lubricants may be easily contaminated. It is also beneficial for sliding motion applications such as plain and spherical bearings, flap tracks, hinges, threads, cam surfaces, etc. The cured lubricant film is highly resistant to conventional fluid lubricants. The process should not be used on materials adversely affected by exposure to temperatures of 302F for 1 hour; on bearings containing rolling elements; or where there is potential contact with liquid oxygen
Masking
Masking is performed on many of the parts we process using a variety of means for selectively coating the hardware. Paints, waxes, tapes, plugs, mechanical masks, and even other finishes are used to protect the areas which are to be free from plating, anodizing, or other finishes.
For further information about how our Chromic Anodizing, Sulfuric Anodizing, Solid Film or Hard Coat Anodizing can improve your next project, contact us or request a quote (you can upload a schematic).